Research Projects
Artificial Intelligence : Autonomous Maritime Maneuvering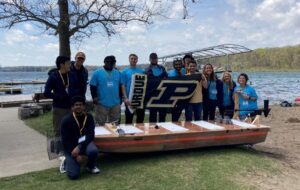
Six universities in Indiana will be competing in an artificial intelligence maritime maneuvering robotic challenge designed by the US Naval Surface Warfare Center and Trine University in April 2025. The team will be provided with a 12 ft unmanned boat, sensor packages, and compute power. The students will be integrating the sensors provided and those purchased to autonomously navigate the boat through a series of challenges. This will provide in-depth learning on machine learning, robotic navigation (ROS), computer vision, artificial intelligence, circuits, mechatronics, mechanics, and naval engineering. Ther are no citizenship requirements for this project. More information about the challenge can be found at AIMM ICC (trine.edu)
Sensors for Industrial ApplicationsMachine systems are the drivers of manufacturing, industries, and everyday devices. These system drive our economy, but can also be the source of safety issues. No matter how complex, machine systems are composed of basic integral building components, including such items as hoses, seals, bearings, and couplers. Each piece must function in order for the machine to operate safely and effectively. In a world where the future will be more reliant upon robotics, machine learning, and autonomous devices, monitoring each component in a complex system becomes critical. The goal of this work is to create an integrated system that monitors numerous system components include items such as belts, seals, hoses, and numerous others to predict pending failure prior to its occurrence and the location of the pending event increasing safety and decreasing cost.
Electroactive PolymersElectroactive polymers represent a class of materials capable of reallocating their shape in response to an electric field and can harvest energy in the form of electrical energy when the materials are mechanically deformed. Electroactive polymers can be used to detect deflection, material changes, pressure changes, or torsional movements. Alternatively, electroactive polymers can also be utilized as energy harvesting devices by storing the energy from mechanical movements in electrical form. These materials can also in turn, be used as actuators to respond to a sensed stimulus from a capacitive signal. Therefore, applications of these materials have a broad range of uses, from components such as smart seals and hoses to micro-pumps, wearable sensors, energy harvesters, and artificial muscles. The goal of this research is to develop a manufacturing process for production of flexible electroactive polymers to enable production of these commercial products.
With the expansion of research and development of fluid power in many industries, it is important that the youth of the next generation be able to understand it’s applications. In order to do this, scientists and researchers must promote outreach to young students. Hence, the Electro-Hydraulic Excavator (EHE) was created to accomplish this goal and demonstrate the real-life application of fluid power. This paper describes, criticizes, and evaluates the design of the Electro-hydraulic Excavator’s (EHE) past iterations and, primarily, it’s current state.
Past Projects
Energy LiteracyEnergy literacy is a critical topic in future business, industry, and global relations. As such, the next generation of engineers, scientists, technologists and policymakers must gain a technical understanding of these issues to advocate and innovate for solutions. Fundamentals of energy conversion are the keystones to student understanding across multiple sub-disciplines in engineering and engineering technology. Energy conversion is the common theme that links thermodynamics, fluid power, electricity, electromagnetism, hydraulics, mechanics, dynamics and numerous other engineering topics. The goal of this work is to horizontally and vertically integrate energy throughout the Mechanical Engineering Technology Curriculum.
Internet-Based Remote Operated RobotsThe Internet of Things is a new trend in technology that is already changing the world in which we live by interconnecting physical objects that can collect or transmit information to us and to each other. This project showcases the use of the IoT by the development of a semi- autonomous utility vehicle using off-the-shelf home automation (smart) components. The system is composed of hardware and software elements that are integrated into a self-propelled scaled down version of an off-road vehicle, a lawn mower. A web application was built and enabled for Android devices to command and control the vehicle, various applets in the application were enabled to be triggered using the Alexa Voice Service and an Amazon Tap speaker. Ultrasonic sensors installed on the vehicle proved their reliability by stopping the vehicle at an average distance of 7.3 cm away from different obstacles. This work contributes to existing knowledge on the Internet of Things by providing a demonstration of a semi-autonomous vehicle capable of cloud-based control both with voice commands and through a web app.
High- resolution 3-D printing (photo-cured polymers) are used for producing various functional plastic components that can be disassembled and reassembled for the practical demonstrations. The components are made transparent so that the students using the components in a kit can observe the movement of the working fluid. Selected prototypes have been designed, built and tested. Various components have been built, this includes, gear type pumps, poppet and spool style valves, and flexible actuators.