February 13, 2018
All-terrain microbot moves by tumbling over complex topography
WEST LAFAYETTE, Ind. – A new type of all-terrain microbot that moves by tumbling could help usher in tiny machines for various applications.
The “microscale magnetic tumbling robot,” or μTUM (microTUM), is about 400 by 800 microns, or millionths of a meter, smaller than the head of a pin. A continuously rotating magnetic field propels the microbot in an end-over-end or sideways tumbling motion, which helps the microbot traverse uneven surfaces such as bumps and trenches, a difficult feat for other forms of motion.
“The μTUM is capable of traversing complex terrains in both dry and wet environments,” said David Cappelleri, an associate professor in Purdue University’s School of Mechanical Engineering and director of Purdue’s Multi-Scale Robotics and Automation Lab.
Findings are detailed in a research paper published online Feb. 3 in the journal Micromachines. The paper was authored by Purdue graduate student Chenghao Bi; postdoctoral research associate Maria Guix; doctoral student Benjamin V. Johnson; Wuming Jing, an assistant professor of mechanical engineering at Lawrence Technological University; and Cappelleri.
The flat, roughly dumbbell-shaped microbot is made of a polymer and has two magnetic ends. A non-magnetic midsection might be used to carry cargo such as medications. Because the bot functions well in wet environments, it has potential biomedical applications. A YouTube video is available at https://www.youtube.com/watch?v=obwvH78hGLY.
“Robotics at the micro- and nano-scale represent one of the new frontiers in intelligent automation systems,” Cappelleri said. “In particular, mobile microrobots have recently emerged as viable candidates for biomedical applications, taking advantage of their small size, manipulation, and autonomous motion capabilities. Targeted drug delivery is one of the key applications of these nano- and microrobots.”
Drug-delivery microbots might be used in conjunction with ultrasound to guide them to their destination in the body.
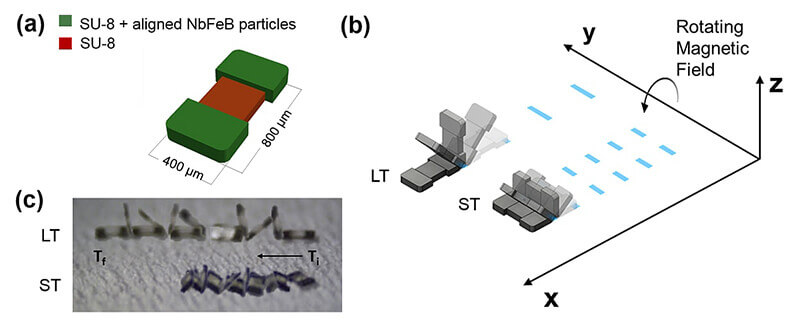
Researchers studied the machine’s performance when traversing inclines as steep as 60 degrees, demonstrating an impressive climbing capability in both wet and dry environments.
“The ability to climb is important because surfaces in the human body are complex,” Guix said. “It’s bumpy, it’s sticky.”
The ideal technology for many applications would be an untethered microrobot that is adaptable to various environments and is simple to operate. Microbots animated through magnetic fields have shown promise, Cappelleri said.
While concepts explored thus far have required complex designs and microfabrication methods, the μTUM is produced with standard photolithography techniques used in the semiconductor industry. The new paper focuses on the microrobot design, fabrication, and use of rotating magnetic fields to operate them in a strategy to negotiate complex terrains.
One critical factor in the development of such microbots is the effect of electrostatic and van der Waals forces between molecules that are prevalent on the scale of microns but not on the macroscale of everyday life. The forces cause "stiction" between tiny components that affect their operation. The researchers modeled the effects of such forces.
“Under dry conditions, these forces make it very challenging to move a microbot to its intended location in the body,” Guix said. “They perform much better in fluid media.”
Because the tiny bots contain such a small quantity and surface area of magnetic material, it takes a relatively strong magnetic field to move them. At the same time, biological fluids or surfaces resist motion.
“This is problematic because for microscale robots to operate successfully in real working environments, mobility is critical,” Cappelleri said.
One way to overcome the problem is with a tumbling locomotion, which requires a lower magnetic-field strength than otherwise needed. Another key to the bot’s performance is the continuously rotating magnetic field.
“Unlike the microTUM, other microscale robots use a rocking motion under an alternating magnetic field, where contact between the robot and the surface is continually lost and regained,” Bi said. “Though the continuously rotating field used for the μTUM is harder to implement than an alternating field, the trade-off is that the tumbling robot always has a point in contact with the ground, provided that there are no sharp drop-offs or cliffs in its path. This sustained contact means that the μTUM design can take advantage of the constant adhesion and frictional forces between itself and the surface below it to climb steep inclined terrains.”
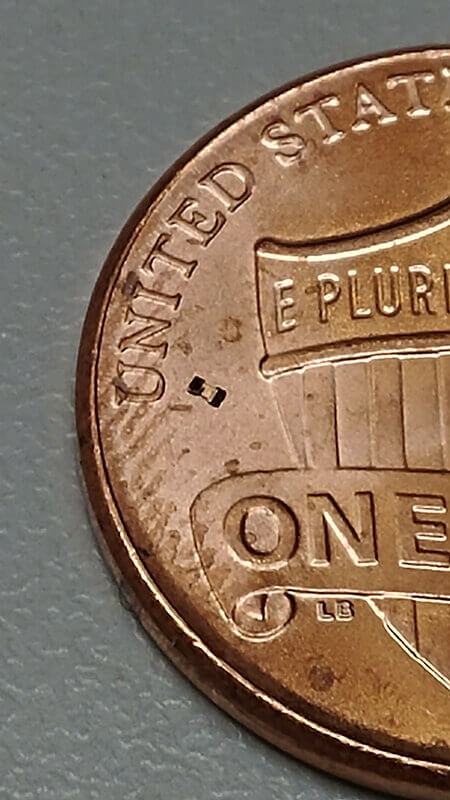
The microbot was tested on a dry paper surface, and in both water and silicone oil to gauge and characterize its capabilities in fluid environments of varying viscosity. Findings showed highly viscous fluids such as silicone oil limit the robot’s maximum speed, while low-density media such as air limit how steep they can climb.
The microTUM might be upgraded with “advanced adhesion” capabilities to perform drug-delivery for biomedical applications.
Future work will focus on dynamic modeling of the μTUM to predict its motion trajectories over complex terrains, as well as addressing the unique challenges present at the interface of distinct environments. Additional goals include developing a “vision-based” control system that uses cameras or sensors for precise navigation and for using such bots to finely manipulate objects for potential industrial applications. Alternate designs for the mid-section of the robot will be explored as well.
“For all the design configurations considered, the midsection of the robot was kept non-magnetized in order to explore the future possibility of embedding a payload in this area of the robot,” Cappelleri said. “Replacing this area with a compliant material or a dissolvable payload could lead to improved dynamic behavior, and in-vivo drug delivery, respectively, with far-reaching potential in micro-object manipulation and biomedical applications.”
Some of the research was performed in the Birck Nanotechnology Center in Purdue’s Discovery Park. The research was funded by the National Science Foundation (NSF IIS Award 1149827).
Writer: Emil Venere, 765-494-4709, venere@purdue.edu
Source: David Cappelleri, 765.494.3719, dcappell@purdue.edu
Note to Journalists: The research paper is available at http://www.mdpi.com/2072-666X/9/2/68 or from Emil Venere, Purdue University News Service, 765-494-4709. venere@purdue.edu. Chenghao Bi is pronounced Chain-How Bee. Maria Guix is pronounced Maria Geesh. A YouTube video is available at https://www.youtube.com/watch?v=obwvH78hGLY. The video was prepared by Jared Pike, communications specialist in Purdue’s School of Mechanical Engineering, jaredpike@purdue.edu.
ABSTRACT
Design of Microscale Magnetic Tumbling Robots for Locomotion in Multiple Environments and Complex Terrains
Chenghao Bi 1, Maria Guix 1, Benjamin V. Johnson 1, Wuming Jing 2, and David J. Cappelleri 1
1 School of Mechanical Engineering, Purdue University, West Lafayette, IN, USA; bi10@purdue.edu (C.B.); mguixnog@purdue.edu (M.G.); john1360@purdue.edu (B.V.J.); dcappell@purdue.edu (D.J.C.)
2 A. Leon Linton Dept. of Mechanical Engineering, Lawrence Technological University, Southfield, MI, USA; wjing@ltu.edu (W.J.)
* Correspondence: dcappell@purdue.edu; Tel.: +1-765-494-3719
This paper presents several variations of a microscale magnetic tumbling (μTUM) robot capable of traversing complex terrains in dry and wet environments. The robot is fabricated by photolithography techniques and consists of a polymeric body with two sections with embedded magnetic particles aligned at the ends and a middle nonmagnetic bridge section. The robot’s footprint dimensions are 400 x 800 μm. Different end geometries are used to test the optimal conditions for low adhesion and increased dynamic response to an actuating external rotating magnetic field. When subjected to a magnetic field as low as 7 mT in dry conditions, this magnetic microrobot is able to operate with a tumbling locomotion mode and translate with speeds of over 60 bodylengths/s (48 mm/s) in dry environments and up to 17 bodylengths/s (13.6 mm/s) in wet environments. Two different tumbling modes were observed and depend on the alignment of the magnetic particles. A technique was devised to measure the magnetic particle alignment angle relative to the robot’s geometry. Rotational frequency limits were observed experimentally, becoming more prohibitive as environment viscosity increases. The μTUM’s performance was studied when traversing inclined planes (up to 60°), showing promising climbing capabilities in both dry and wet conditions. Maximum open loop straight-line trajectory errors of less than 4% and 2% of the traversal distance in the vertical and horizontal directions, respectively, for the μTUM was observed. Full directional control of μTUM was demonstrated through the traversal of a P-shaped trajectory. Additionally, successful locomotion of the optimized μTUM design over complex terrains was also achieved. By implementing machine vision control and/or embedding of payloads in the middle section of the robot, it is possible in the future to upgrade the current design with computer-optimized mobility through multiple environments and the ability to perform drug delivery tasks for biomedical applications.