October 3, 2018
New 3D-printed cement paste gets stronger when it cracks — just like structures in nature
WEST LAFAYETTE, Ind. — What if the inherent weaknesses of a material actually made houses and buildings stronger during wildfires and earthquakes?
Purdue University researchers have 3D-printed cement paste, a key ingredient of the concrete and mortar used to build various elements of infrastructure, that gets tougher under pressure like the shells of arthropods such as lobsters and beetles. The technique could eventually contribute to more resilient structures during natural disasters.
"Nature has to deal with weaknesses to survive, so we are using the 'built-in' weaknesses of cement-based materials to increase their toughness," said Jan Olek, a professor in Purdue's Lyles School of Civil Engineering.
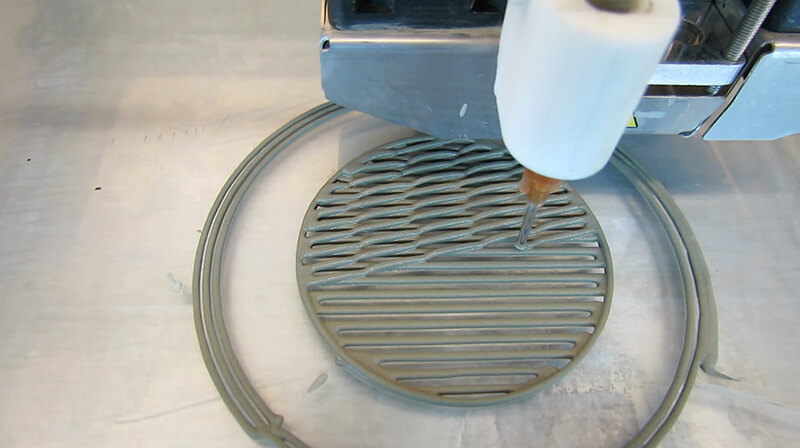
The idea would be to use designs inspired by arthropod shells to control how damage spreads between the printed layers of a material, like trying to break a bunch of uncooked spaghetti noodles as opposed to a single noodle.
"The exoskeletons of arthropods have crack propagation and toughening mechanisms that we can reproduce in 3D-printed cement paste," said Pablo Zavattieri, Purdue professor of civil engineering.
3D-printed cement-based materials – such as cement paste, mortar and concrete – would give engineers more control over design and performance, but technicalities have stood in the way of scaling them up.
Purdue engineers are the first to use 3D printing to create bioinspired structures using cement paste, as shown in a published paper and the frontispiece for an upcoming print issue of the journal Advanced Materials.
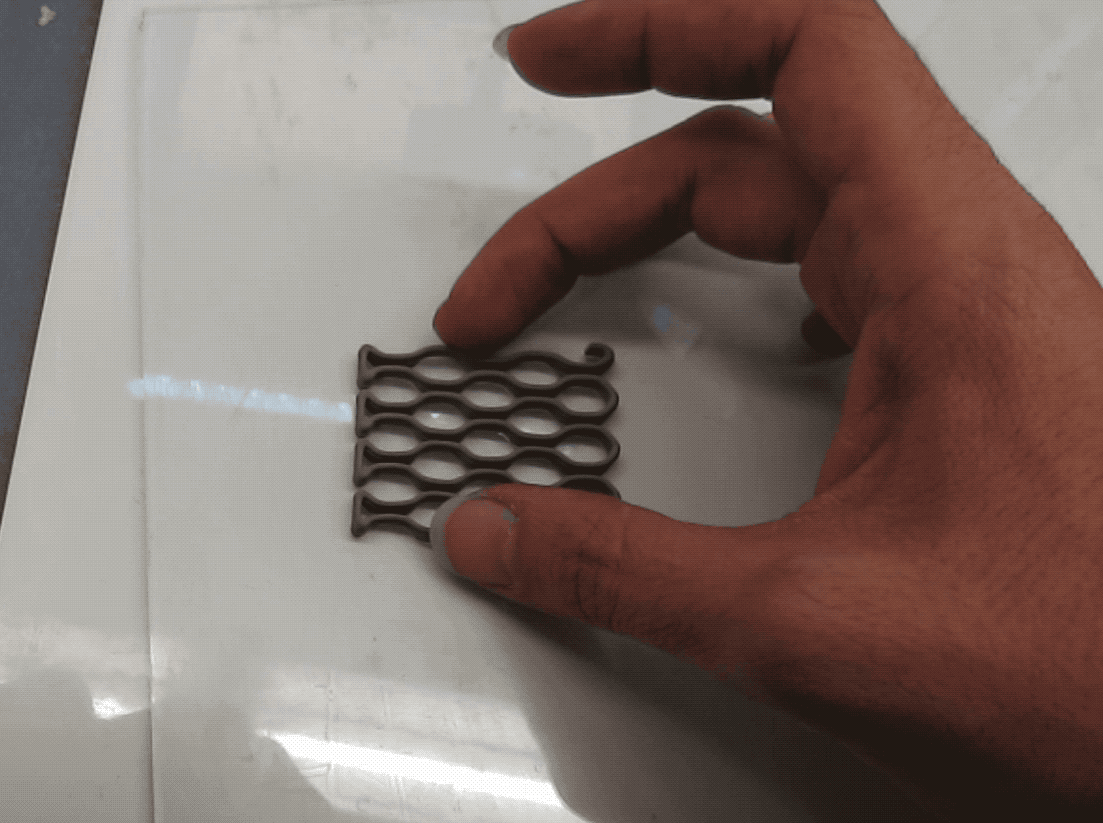
"3D printing has removed the need for creating a mold for each type of design, so that we can achieve these unique properties of cement-based materials that were not possible before," said Jeffrey Youngblood, Purdue professor of materials engineering.
The team is also using micro-CT scans to better understand the behavior of hardened 3D-printed cement-based materials and take advantage of their weak characteristics, such as pore regions found at the "interfaces" between the printed layers, which promote cracking. This finding was recently presented at the 1st RILEM International Conference on Concrete and Digital Fabrication.
"3D printing cement-based materials provides control over their structure, which can lead to the creation of more damage and flaw-tolerant structural elements like beams or columns," said Mohamadreza "Reza" Moini, a Purdue Ph.D. candidate of civil engineering. Watch a YouTube video at https://youtu.be/Q0MvUdZoejk.
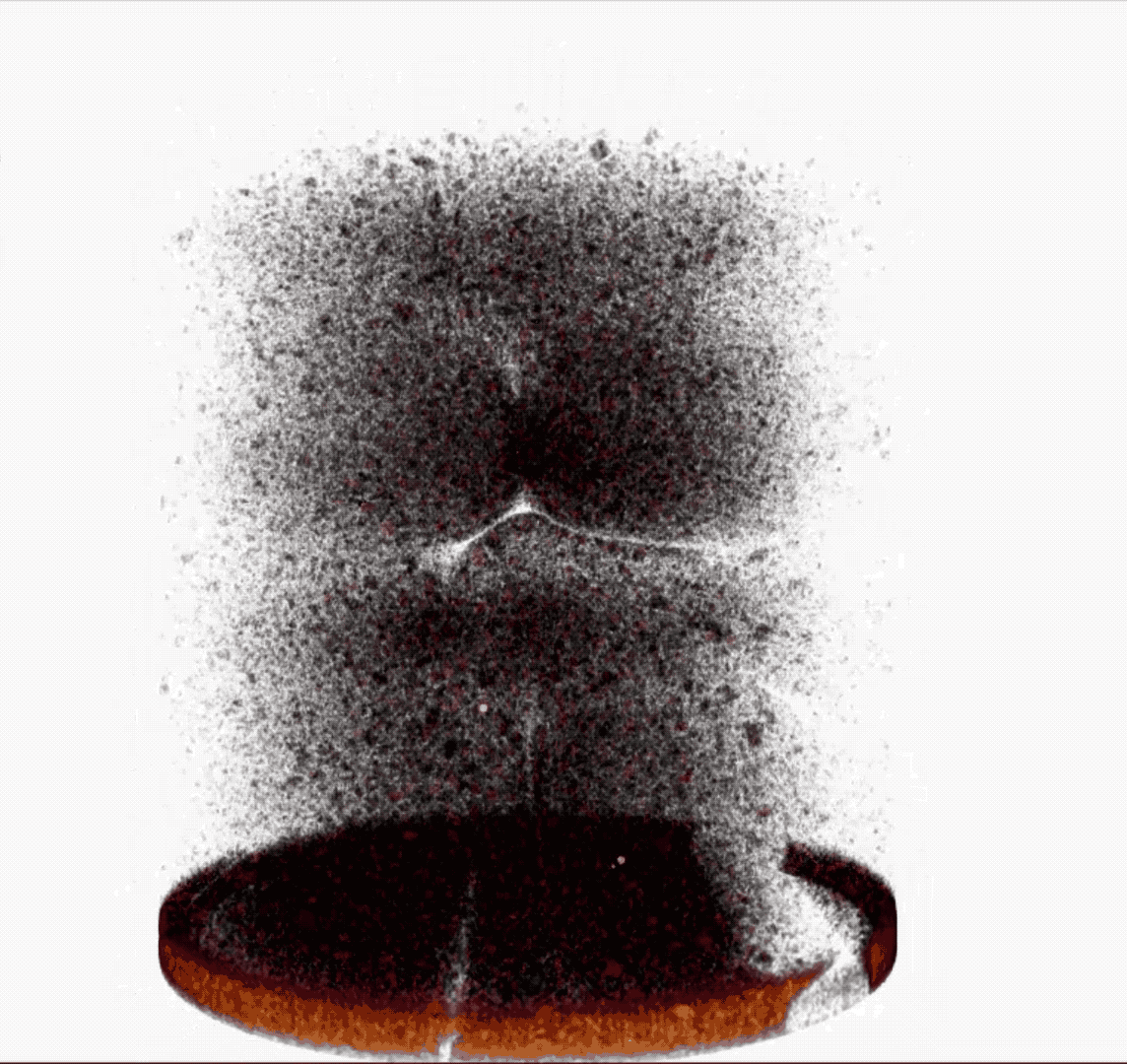
The team was initially inspired by the mantis shrimp, which conquers its prey with a "dactyl club" appendage that grows tougher on impact through twisting cracks that dissipate energy and prevent the club from falling apart.
Some of the bioinspired cement paste elements designed and fabricated by the team using 3D printing techniques include the "honeycomb," "compliant" and "Bouligand" designs, called "architectures."
Each of these architectures allowed for new behaviors in a 3D-printed element once hardened. The Bouligand architecture, for example, takes advantage of weak interfaces to make a material more crack-resistant, whereas the compliant architecture makes cement-based elements act like a spring, even though they are made of brittle material.
The team plans to explore other ways that cement-based elements could be designed for building more resilient structures.
The work was funded by the National Science Foundation (Grant No. CMMI 1562927). The acquisition of the X-ray microscope was supported by the 2017 Major Multi-User Equipment Program, offered by the Office of the Executive Vice President for Research at Purdue University.
Writer: Kayla Wiles, 765-494-2432, wiles5@purdue.edu
Sources:
Reza Moini, 765-494-6634, mmoini@purdue.edu
Pablo Zavattieri, 765-496-9644, zavattie@purdue.edu
Jan Olek, 765-494-5015, olek@purdue.edu
Jeffrey Youngblood, 765-496-2294, jpyoungb@purdue.edu
Note to Journalists: For full-text copies of the papers, please contact Kayla Wiles, Purdue News Service, at wiles5@purdue.edu. A YouTube video is available at https://youtu.be/Q0MvUdZoejk and other multimedia, including photos of each new 3D-printed cement paste design, can be found in a Google Drive folder at http://bit.ly/2O2c9Cd. The materials were prepared by Erin Easterling, digital producer for the Purdue College of Engineering, 765-496-3388, easterling@purdue.edu
Additive manufacturing and performance of architectured cement-based materials
Mohamadreza Moini1, Jan Olek1, Jeffrey Youngblood1, Bryan Magee2, Pablo Zavattieri1
1Purdue University, West Lafayette, IN, USA
2Ulster University, Newtonabbey, UK
doi: 10.1002/adma.201802123
There is an increasing interest in hierarchical design and Additive Manufacturing (AM) of cement-based materials. However, the brittle behavior of these materials and the presence of interfaces from the additive manufacturing process represent the current major challenges. Contrary to the commonly adopted approach in AM of cement-based materials to eliminate the interfaces and to add reinforcements, our work focuses on harnessing the heterogeneous interfaces by employing clever designs from bio-inspired Bouligand architectured materials. In this paper, we aim to demonstrate some key mechanisms that can allow brittle hardened cement-based materials to gain flaw-tolerant properties. Mechanisms such as crack twisting at the interfaces have been previously observed in naturally-occurring or synthetic composite Bouligand architectures. In this paper, a heterogeneous interface with porous characteristics in 3D-printed solid hardened cement paste (hcp) architectures were characterized. We hypothesize that the presence of heterogeneous interface in 3D-printed hardened cement paste (hcp) elements, in conjunction with clever architectures, promote key damage mechanisms such as interfacial cracking and crack twisting that lead to damage delocalization. This delocalization can be energetically favorable and allow energy dissipation and promote toughening and flaw-tolerant properties. These mechanisms can be controlled through AM
and design of the architecture of hcp materials and can play a role in tuning, enhancing and diversifying the mechanisms that improve work of failure, strength, and inelastic deflection of the structure. The evidence is provided by multiaxial flexural tests comparing the architectured materials with cast specimens. We found that these architectures can enhance the properties from the typical strength-porosity relationship, classically known for brittle hcp materials. In turn, these architectures exhibit 1 interfacial damage mechanisms and demonstrate improvements of the work of failure by more than 50% exhibiting the controlled spread of damage without sacrificing strength.
Additive manufacturing and characterization of architecture cement-based materials via x-ray micro-computed tomography
Mohamadreza Moini1, Jan Olek1, Bryan Magee2, Pablo Zavattieri1, Jeffrey Youngblood1
1Purdue University, West Lafayette, IN, USA
2Ulster University, Newtonabbey, UK
doi: 10.1007/978-3-319-99519-9_16
There is an increasing interest in the fabrication of cement-based materials via additive manufacturing (AM) techniques. However, the processing-induced heterogeneities and interfaces represent a major challenge. The role of processing in creating interfaces and their characteristics requires understanding of the microstructure of 3D-printed hardened cement paste (hcp). This work investigates the microstructural features of architectured cement-based materials, including processing-induced heterogeneous patterns, interfacial regions (IRs), and pore network distributions with respect to the architectural pattern. A 3D printer was modified and merged with an extrusion system and specimens were 3D-printed using a layer-wise direct ink writing (DIW) process capable of fabrication of ‘lamellar' architectures of materials. A lab-based X-ray microscope (XRM) was used to perform X-ray micro-computed tomography (micro-CT) evaluations to explore the microstructural characteristics of 3-day old intact (i.e. not tested) 3D-printed and cast specimens at two levels of magnification: 0.4X and 4X. CT scans of printed specimen revealed a patterned pore network and several microstructural features, including: a) macropores (visible during printing), b) micropores at interfacial regions (IRs), c) accumulation of anhydrous cement particles near macropores, and d) rearrangement of filaments away from their designed toolpath. In comparison, microstructural investigation of cast specimen at 4X scan revealed randomly distributed pores with no connectivity throughout the specimen. The aptitude of micro-CT as a non-destructive technique for microstructural characterization of architectured cement-based materials is discussed. The role of processing to induce and to pattern heterogeneities such as IRs in materials is demonstrated and the role of architecture in controlling such heterogeneities and their directionality through the interface is discussed.