PARI hypersonics manufacturing facility wraps up contract, builds momentum for the future
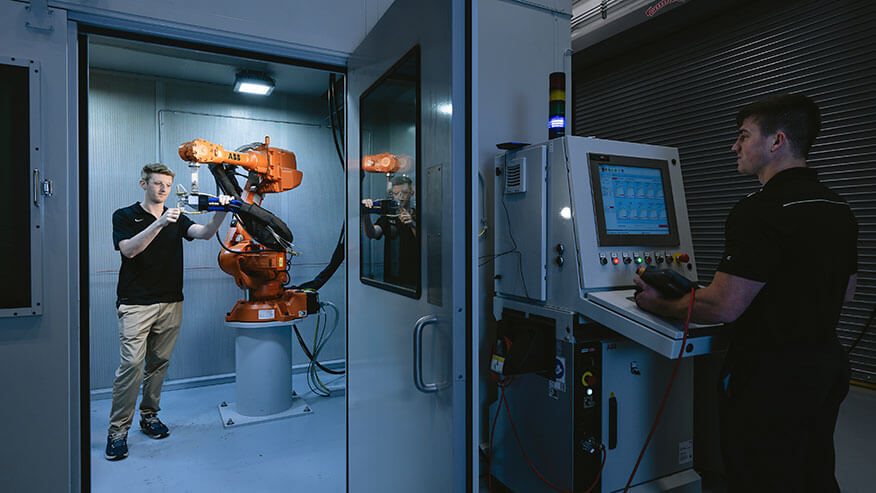
WEST LAFAYETTE, Ind. — The Purdue Applied Research Institute’s (PARI) flagship hypersonics manufacturing facility completed its original 30-month, $18.6 million contract. To kick off its next phase, the Hypersonics Advanced Manufacturing Technology Center (HAMTC) leadership is building on the successes of its first two years by further establishing a pipeline of customers, collaborators and talent to bolster the hypersonics manufacturing industry.
“The completion of the HAMTC contract marks PARI and Purdue, together, as a leader in hypersonics research and development,” said Greg Scofield, director of PARI’s Hypersonic Lab, who oversees HAMTC. “We’re touching the entire hypersonics supply chain — from design and manufacturing to validation, verification and all the way to testing — and working closely with all of our partners in that process.”
Vertical integration of the hypersonics manufacturing process
In its first two years, HAMTC’s faculty, staff and students have succeeded in setting up a vertically integrated facility where researchers and practitioners design, manufacture, join and test hypersonic systems and components, all in one location.
“Our facility is fully operational and ready to support industry needs,” Scofield said. “With a vertically integrated setup, we can significantly reduce the time required to develop and manufacture prototypes for new designs and advance them through ground testing. Our team and resources are equipped and ready to deliver these capabilities efficiently and effectively.”
Materials and assembly are crucial to a functioning hypersonic vehicle. A hypersonic aircraft’s speed generates intense friction with the atmosphere and exposes the vehicle to extreme conditions, creating unique engineering challenges.
HAMTC has been instrumental in tackling these obstacles, particularly by pioneering new manufacturing methods for hypersonic vehicle components. A standout achievement is HAMTC’s progress in additive manufacturing, also known as 3D printing.
According to Mark Lewis, president and CEO of PARI, additive manufacturing of hypersonics offers a distinct advantage over traditional methods.
“Conventional manufacturing typically involves starting with a solid block of metal and machining it down to the desired shape, a process that can waste material and which has limits to the complexity of the final shape,” Lewis said. “In contrast, additive manufacturing builds components layer by layer, enabling the creation of intricate designs, including internal geometries such as cooling channels, with less wasted material.”
HAMTC’s most impressive additive manufacturing feat thus far is its full-scale, 3D printed scramjet, an engine that allows aircraft to travel at speeds of Mach 5 and beyond. A team of PARI students used advanced additive manufacturing techniques to successfully design, manufacture and test a scramjet comparable in size to the X-51A Waverider.
Lewis said the scramjet project highlights PARI’s unique capability to handle hypersonic projects from conception to testing in a single location while at the same time training the next generation of the hypersonics workforce. This achievement also demonstrates the potential for more efficient and cost-effective manufacturing processes, which would remove barriers to hypersonic production for the defense industry.
“Hypersonic systems have thus far been more expensive than lower-speed counterparts, in part because of the materials and the manufacturing costs,” Lewis said. “So, what HAMTC is aiming to do is develop a whole new way to reduce the cost of manufacturing and get these vehicles at price points that are comparable to other defense systems, which would then ramp up production and deployment.”
HAMTC has also made strides in ceramic additive manufacturing through research on 3D printing dark ceramics, materials that can withstand the harsh conditions of hypersonic flight due to their high melting temperatures, strength and ability to resist degradation.
Led by Rodney Trice, professor of materials engineering and thrust lead in ceramic processing at HAMTC, this project employs digital light processing, a method that uses UV light to cure thin layers of ceramic powder mixed with resin, enabling intricate designs with micron-level precision. Trice, ceramics research engineer Dylan Crump, and materials engineering doctoral candidate Matthew Thompson have begun printing these novel materials on a one-of-a-kind, large-format prototype ceramic printer housed at HAMTC.
Additional Background Information:
Looking to the future
As HAMTC moves into its next phase, the center’s leadership is building off its initial successes and expanding its funding, partnerships and capabilities.
The center’s latest funding efforts include a $1.2 million test and evaluation initiative with the Air Force Office of Scientific Research and a portion of a $1.45 billion award led by Kratos Defense & Security Solutions Inc. to develop a cost-effective flight test bed designed to quickly expand the nation’s hypersonic flight-testing capabilities.
In terms of partnerships, David Bretz, HAMTC’s senior project manager, sees potential in replicating HAMTC’s arrangement with Colibrium Additive, a GE Aerospace Company, where two of its engineers are embedded into the center’s everyday operations to provide on-sight support for all aspects of the additive manufacturing process.
“Through this agreement with Colibrium Additive, we’ve demonstrated our ability to integrate industry professionals into the PARI ecosystem,” Bretz said. “We’re able to get them Purdue credentials, which gives them uninhibited access to our state-of-the-art facilities and our talented faculty, staff and students.”
Scofield and Bretz also want to emphasize that HAMTC is available to faculty members, as the center can help them transition their research to industry or government.
“HAMTC has opened the door to new collaborations internally at Purdue,” Scofield said. “We have faculty members from a variety of colleges and schools working directly with PARI now in large part because of our facilities.”
For example, Luz Sotelo, assistant professor of mechanical engineering, used HAMTC’s X-ray computed tomography (CT) machine to “see inside” small stainless-steel cubes to learn how to nondestructively detect voids and defects in a solid metal part.
“This CT is super helpful to my research,” Sotelo said, “because it offers a ground truth that I can use to improve the algorithms and processing behind my ultrasonic imaging. If the HAMTC facility didn’t exist, I would have to ship these samples somewhere to get imaged, which would take a long time.”
About Purdue University
Purdue University is a public research university leading with excellence at scale. Ranked among top 10 public universities in the United States, Purdue discovers, disseminates and deploys knowledge with a quality and at a scale second to none. More than 107,000 students study at Purdue across multiple campuses, locations and modalities, including more than 58,000 at our main campus in West Lafayette and Indianapolis. Committed to affordability and accessibility, Purdue’s main campus has frozen tuition 13 years in a row. See how Purdue never stops in the persistent pursuit of the next giant leap — including its comprehensive urban expansion, the Mitch Daniels School of Business, Purdue Computes and the One Health initiative — at https://www.purdue.edu/president/strategic-initiatives.
Media contact: Lindsey Macdonald, macdonl@purdue.edu